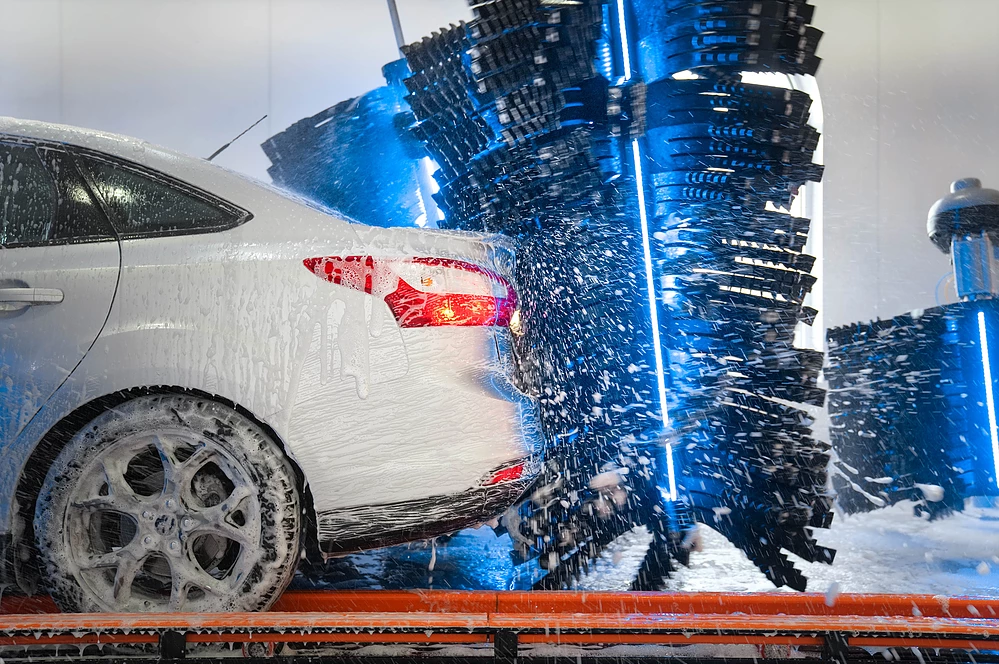
In early 2020, the International Carwash Association reported the findings from its first-ever comprehensive study designed to define the size and scope of the United States carwash industry.
And to paraphrase every U.S. President who has given a “State of the Union” address over the past 40 years: “The state of the tunnel-wash segment is good.”
The study showed that of all retail vehicle-wash locations in the U.S, 27.9% are conveyorized-tunnel locations. In-bay automatics/rollovers have the largest market share with 46.3%, while self-service sites account for 25.8% of vehicle-wash locations.
The relatively strong showing of tunnel washes – which are actually celebrating their 80th anniversary this year, with the first one built in Hollywood, CA, in 1940 – is made more impressive by the fact that they have some built-in hurdles to adoption that must be addressed and overcome, including:
- Higher purchase and installation costs than in-bay automatics or self-service systems
- A larger footprint, even for the increasingly popular mini-tunnel versions, that requires more on-site real estate
- Many need a staff to man them, which will increase labor costs for the operator
Despite this, tunnel washes continue to forge ahead and have made a comfortable home for themselves in the vehicle-wash universe. One trend within the ICA study that portends further success is the fact that more and more drivers are opting to have their vehicles washed for them instead of doing it themselves. The report indicates that in the U.S., the percentage of drivers that are most frequently having their vehicles washed professionally has risen to 77% from 48% in 1994.
Since 1969, Belanger, Inc., has been a leader in developing innovative tunnel-wash designs that are able to deliver a better wash experience for the customer and the highest level of reliability, durability and serviceability for the operator. Belanger currently offers two types of conveyorized-tunnel systems to the market:
- Classic Conveyorized: Belanger built the industry’s first soft-touch tunnel system and its current classic conveyorized units draw on decades of engineering know-how to carry on that proud tradition. The system is built with an aircraft-grade aluminum frame that ensures long-life performance, while a minimum number of moving parts reduce breakdown risks, and if a service disruption should occur, the offending part is easy to identify and repair or replace. Full tunnels have the capability to wash upwards of 200 vehicles an hour, which is one of the highest throughout rates in the industry. Innovative options include the DuraTrans® XD conveyor, Sudzer® BL application arch, Whisper Wheel® top wheel, QuickFire® wrap-around, DuraShiner® CV programmable tire dresser and a full line of touchless dryers.
- SpinLite: Belanger’s latest tunnel-system innovation, SpinLite allows tunnel-wash operators to offer something a little “different” to their customers, namely a quieter wash experience that equates to a fun, relaxing trip through the tunnel, where a clean, dry, shiny vehicle emerges. Specifically, ShineMitt slow-spinning wash wheels feature a wash media that alleviates the risk of vehicle damage while simultaneously delivering a quieter, more efficient wash experience. The ShineMitt secret is a self-supporting brush design that allows the wash wheels to spin slower while still enabling the soft-touch “fingers” to access hard-to-reach vehicle contours, resulting in a cleaner vehicle. SpinLite customizable options include DryLite dryers, AIRIS air-flow management system, H2Air rinse arch and Durameleon Plus lighting and chemical-application system.
A combination of a strong installed base and the desire of more and more drivers to have their vehicles professionally washed indicates that the future is bright for the tunnel-wash market segment. Belanger stands ready to assist the operators in this important vehicle-wash niche with cutting-edge tunnel-wash systems that consistently and reliably meet the needs of drivers and vehicle-wash operators.